What Is Electrical Discharge Machining (EDM) Cutting? | Blog Posts | OneMonroe
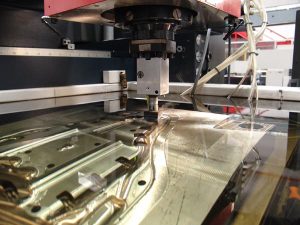
There are a variety of cutting processes used in the manufacturing industry. While you might be familiar with laser, plasma and water jet, a lesser-known cutting process is electrical discharge machining (EDM). It’s a metal fabrication technique that allows manufacturing companies to easily cut through metal workpieces. EDM cutting, however, is a highly advanced process that’s distinguished from other cutting processes in several ways.
Overview of EDM Cutting
Also known as spark machining cutting, EDM cutting is a cutting process that involves the use of electrical discharge to slice through metal workpieces. Electrical discharges are sparks. With EDM cutting, a machine produces controlled sparks that vaporize or melt areas of the metal workpiece with which it’s used.
How EDM Cutting Works
Although there are different ways to perform it, all EDM cutting processes require the use of an EDM machine. An EDM machine is a machine that’s capable of producing electrical discharges. It features a pair of electrodes. One of these electrodes is known as a “tool electrode,” whereas the other is known as a “workpiece electrode.”
The metal workpiece is placed between these two electrodes. When the EDM machine is engaged, it will produce electrical discharges between the tool electrode and the workpiece electrode, thereby striking the metal workpiece with sparks. These sparks will essentially vaporize or melt the workpiece, which is how EDM cutting works. As the material vaporizes or melts, the metal workpiece’s shape and size will change.
Benefits of EDM Cutting
There are several benefits of EDM cutting. For starters, it’s able to create clean and precise cuts. Many manufacturing companies, in fact, use EDM cutting to produce die sets for this reason. Regardless of the size or shape of a die set, EDM cutting will probably support it.
Another benefit of EDM cutting is that it protects workpieces from direct damage. There’s no physical contact between EDM machines and the metal workpieces with which they are used. Rather, the electrodes of an EDM machine are placed away from workpieces. Without any physical contact between the electrodes and the workpieces, EDM cutting is a safer process than traditional cutting processes.
EDM cutting supports tapered holes. Manufacturing companies often use it to create tapered holes in metal workpieces. Tapered holes are those that become narrower or wider. While tapered holes can be produced using other cutting processes, they are easier to produce with EDM cutting. EDM cutting can easily create all types of holes, including standard holes as well as tapered holes.
No tags for this post.
No tags for this post.